Down jacket #1
- Xenia
- Dec 23, 2016
- 3 min read
Winter travel in expected 0 to -10 Celsius temperatures prompted me to make my first down jacket.
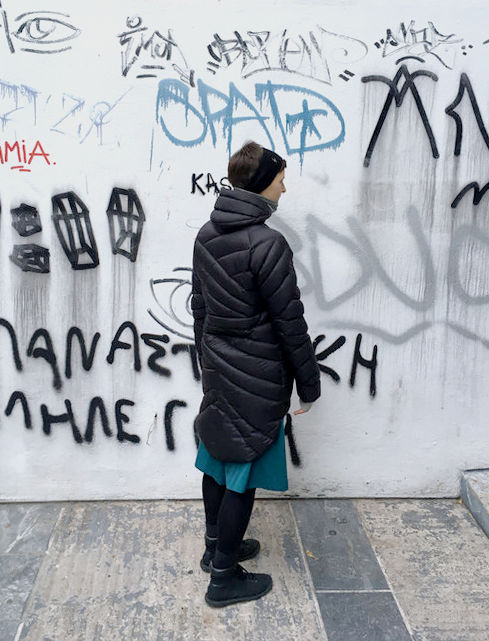
Here is a pic of a completed one, below is a long story about steps of its creation.
Did I have an idea of how thick the down jacket has to be for that temperatures? No. Only very vague feeling. And only vague idea about other important features that are necessary. I learned how to work with down on my own, all the knowledge I have came from rare and scattered semi-related articles over the internet and a process of trials and reiterations. With such a big piece of work as a jacket iterations are costly, so the first attempt have had to bring a decent outcome, which would keep us warm in January in Moscow and in February in Tokyo.
First - ordering supplies, I approximated that I would need about 8 yards of fabric for two thigh-length jackets, this was not hard to figure out, the amount of down needed was trickier to calculate. So I approached it in reversed engineering fashion, I checked out the weight of Patagonia warmest alpine jacket, which was 24 oz. and decided that half of that will do for one jacket. Of course 24 oz. is weight of a whole jacket, but weight of fabric and notions didn't seem to me to be more than 4-5 oz. (which, as I'm thinking now, was a wrong approximation, suppose you use 1 oz./square yard fabric, fabric alone would weigh around 8 oz., add zippers, cords and misc hardware and it could go up to 10 oz.). I ended up using only about 14 oz. of down for both jackets. Of course there would be big difference in amount of down needed for the same length jacket if it would have baffled construction, not stitched through. For extreme temperatures baffled construction is a must, but I decided not to go extreme, especially since it is a first jacket, though I'm curious to try that technique.
Second challenge, the pattern. I adapted my rain coat pattern, but there was a question by how much to lengthen sleeves and bodice to account for down volume. I went a bit too far, adding approx 20% of length, now I would say it should be around 10%. Though curiously enough when I stuffed a completed sleeve and compared its length to a yet unstuffed one it was just 20% shorter.
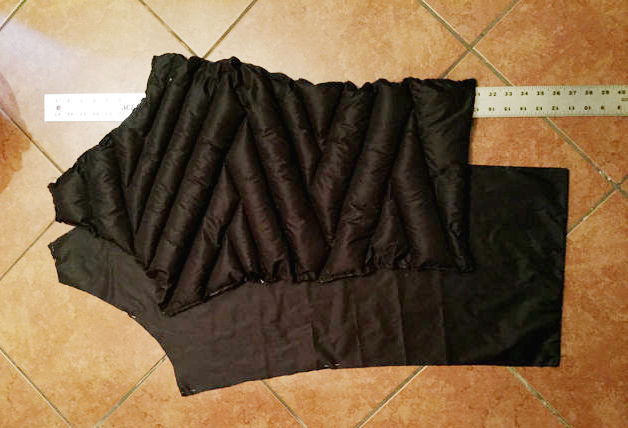
And I was triumphant when measured, but after I assembled whole jacket and tried it on I found out that sleeve piece has lengthened, compared to flat state at rest. Reason, in my understanding, is that sleeve wraps closely around arm and thus stretches along it. As well it might be because of gravity. Another aspect that needs attention while making pattern is seam type used to connect staffed pieces together. I observed that most jackets use bound seam, and binding is cut from the same fabric as a jacket, I decided not to go so elaborate, as binding tape have to be cut on bias and than both edges folded toward the center and ironed and than whole tape folded in half and ironed, besides it would have taken additional yard of fabric and a lot of time to make the tape. I wish I could buy binding tape made from approximately same material, but such thing just doesn't exist. So I chose to use 'french seam', which is also elaborate, but works well.
Third, once you have drafted patterns for all parts, you need to decide how to divide every piece into down channels. Simplest way is to just use horizontal division. Not fun. So I went artistic way: tilted lines, curved lines, lines starting not from edge but from the middle, creating an angle with another line. It added significant amount of time to a stuffing process, mainly because some channels would have open end on one edge of a piece, others on another, so you couldn't just stitch close one edge and stuff from another all of the channels, like on horizontally divided pieces. Another issue was tight corners, when channel would end in a sharp angle, less than 45 degrees, I would have to use small stick (weapon of choice: lacquered chopstick) to guide down all the way to the sharp end without creating a clot.
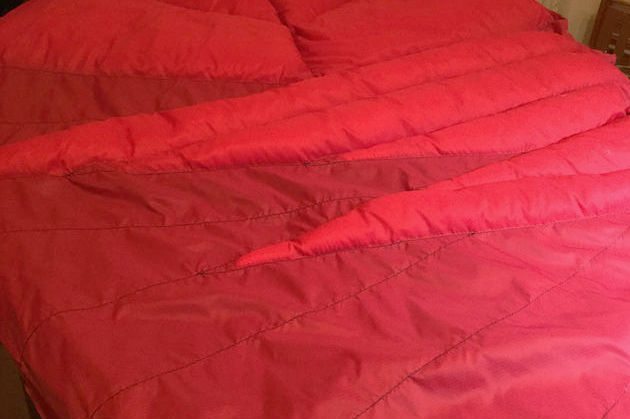
Knowing all of this, second jacket was way less artistically divided into channels. That's a pic of a marking template for the bodice of the second jacket:
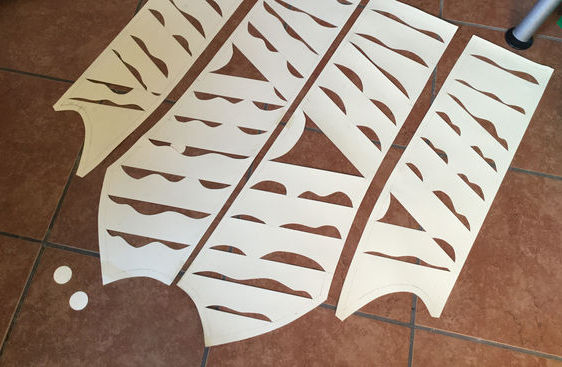
All straight lines you see represents actual seams, all curved lines does not represent anything and I made them curved to avoid confusion when marking fabric. Some straight lines are not continuous from edge to edge, this is also not a representation of seam configuration, if I'd cut all lines from edge to edge paper would become too unstable. I feel that I need to make a pause, since there is more information to share, so I'll divide it and continue in Part 2.
Comments